INTRODUÇÃO:
O LEAN MANUFACTURING foi desenvolvido após a II GUERRA MUNDIAL como um sistemaformado por técnicas simples e eficientes. Nasceu nos setores operacionais da manufatura (o CHÃO DE FÁBRICA).
Mas, a denominação não foi criada na TOYOTA. O termo vem do inglês LEAN (ENXUTA) e MANUFACTURING (MANUFATURA) e foi utilizado pelos estudiosos do MIT (MASSACHUSSETTS INSTITUTE OF TECHNOLOGY) analisando em detalhes as técnicas do sistema de produção e os trabalhos desenvolvidos pelos japoneses. Foi denominado de enxuto pela redução de quantidade, custos e tempo: menos esforço dos funcionários, menos espaço para fabricação, menos investimento em ferramentas, menos tempo de planejamento, menores estoques, menos fornecedores, redução de defeitos e maior variedade de produtos.
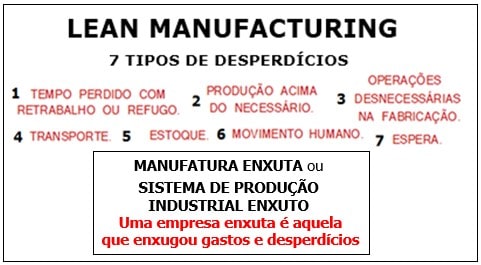
GESTÃO LEAN
O princípio é organizar um processo de trabalho de forma que o desperdício seja mínimo e os recursos sejam utilizados na capacidade ideal para manter a produtividade. A GESTÃO LEAN se tornou uma ferramenta de gestão universal adotada em todos os setores. O seu fundamento é composto por três ideias simples: buscar sempre a melhoria, criar valor e eliminar desperdícios.
AS FERRAMENTAS DO LEAN MANUFACTURING
FERRAMENTAS LEAN: FIVE WHY’S, (5 POR QUES), FILOSOFIA 5S, JIT (JUST IN TIME), MILK RUN, PADRONIZAÇÃO DE ATIVIDADES, MUDA, SMED (SINGLE MINUTE EXCHANGE OF DIE – Troca rápida de Ferramentas ou TRF), KANBAN, KAIZEN,YAMAZUMI,JIDOKA – AUTONOMAÇÃO, HEIJUNKA, TAKT TIME,POKA YOKE, PULL SYSTEM, M&I – FLUXO DE MATERIAIS E INFORMAÇÕES, MAPEAMENTO DE FLUXO E VALOR e PET –PRÁTICAS EMPRESARIAIS TOYOTA.
1 – OS 5 POR QUES
A técnica dos 5 PORQUÊS foi um conceito criado por SAKICHI TOYODA e, posteriormente, utilizada pela TOYOTA. Porém, ela é usada até hoje para resolver problemas, melhorar a qualidade e reduzir desperdícios. Quando ocorre um problema, é preciso perguntar “POR QUE” cinco vezes para tentar encontrar a fonte do problema – encontrar a causa raiz, enfrentar o problema de maneira adequada e tomar uma decisão baseada em uma compreensão criteriosa do que realmente está ocorrendo. Em seguida, atua-se na fonte do problema para eliminá-lo de forma definitiva e prevenir que ocorra novamente. A técnica também é conhecida por FIVE WHY`S.
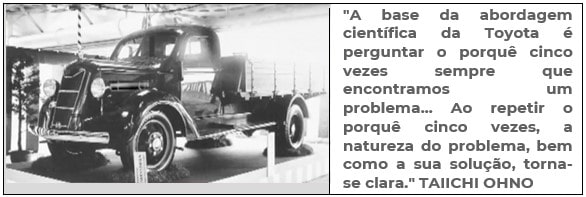
2 – A FILOSOFIA 5S
O LEAN MANUFACTURING usa a METODOLOGIA 5S para conduzir e mobilizar uma organização para a QUALIDADE TOTAL. Foi criado por KAORU ISHIKAWA diante da desorganização e com o ambiente das fábricas em fase de reconstrução no pós-guerra. A FILOSOFIA segue cinco conceitos pelas palavras japonesas que começam com a letra S:
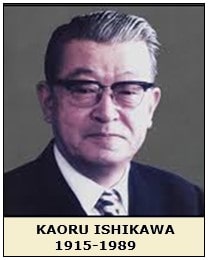
SEIRI (utilização): a ideia é manter somente o que for estritamente necessário no local de trabalho para a tarefa a ser feita.
SEITON (organização): arrumar e organizar o ambiente representando o senso de sistematização e classificação. Prevê um espaço organizado e a disposição de móveis, ferramentas, equipamentos, documentos e objetos em uma sequência lógica. É o que vai permitir o fluxo correto das tarefas, rapidez e facilidade na busca.
SEISO (limpeza): facilita identificar sinais de degradação de recursos, reduz o risco de avarias. É a manutenção da área, dos equipamentos, ambiente de trabalho e processos que faz da limpeza uma parte essencial do trabalho diário e não uma atividade ocasional.
SEIKETSU (saúde e higiene): cuida da higiene sob todos os aspectos (inclusive na ERGONOMIA). Identifica possíveis prejuízos à saúde dos trabalhadores e busca a correção de problemas.
SHITSUKE (autodisciplina): os trabalhadores devem cumprir o que for estabelecido e, ao mesmo tempo, ter autonomia para um comportamento proativo.
3 – JIT (JUST IN TIME)
Este processo tem por finalidade a fabricação sem estoque (ou com o mínimo possível de estoque), buscando qualidade, em tempo menor e com baixo custo. É uma abordagem disciplinada, que combate o desperdício e o retrabalho. A principal ideia do JUST IN TIME está relacionada à PRODUÇÃO POR DEMANDA: primeiro o produto é vendido e, somente depois sua matéria-prima é comprada e o produto fabricado (ao contrário das empresas ocidentais que utilizavam a ECONOMIA DE ESCALA com diminuição do custo por meio do aumento da produção). Desta maneira, o estoque de matérias-primas guarda somente o suficiente para algumas horas de produção.
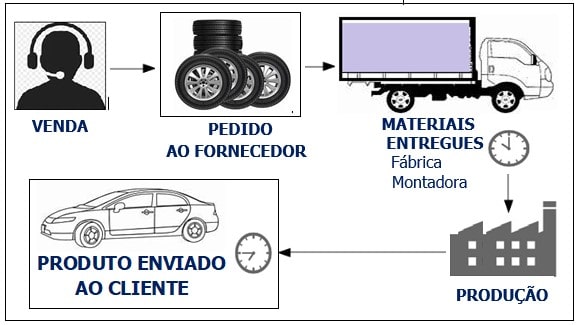
O produto ou matéria prima chega ao local de utilização somente no momento exato para ser enviado a linha de produção. Os produtos só são fabricados ou entregues a tempo de serem vendidos e montados. É uma forma de ADMINISTRAÇÃO DA PRODUÇÃO que estabelece que NADA é produzido, transportado ou comprado antes da hora exata. Pode ser aplicado em qualquer empresa para reduzir o custo do estoque.
Durante os anos 20, KIICHIRO TOYODA havia visitado diversas fábricas de automóveis nos EUA e Europa observando as formas de trabalho. No fim da década de 30, estabeleceu a filosofia para as operações da TOYOTA criando, pela primeira vez, o termo JUST-IN-TIME: um fluxo de materiais contínuo, considerando desde as matérias-primas até o consumidor final.
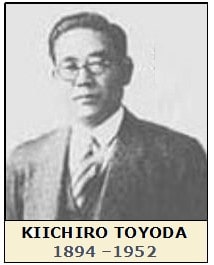
KIICHIRO TOYODA raciocinou que o melhor meio seria ter todas as peças e partes necessárias para a montagem ao lado da linha para serem usadas, exatamente na hora – JUST-IN-TIME.
Ele usou a expressão descrevendo o fluxo contínuo de materiais sincronizado com a programação da produção minimizando a necessidade de estoques. Abrange desde as matérias primas até o consumidor e que se tornaria um dos pilares do LEAN MANUFACTURING.
Em 1948 TAIICHI OHNO realizou os primeiros experimentos em um “SISTEMA PUXADO” com a fabricação em resposta ao “PUXAR” do cliente (pedido). O método JIT,a princípio, teve o objetivo de reconstruir as empresas no pós-guerra. A TOYOTA foi a primeira na utilização da nova ferramenta em 1953 quando OHNO pôs o JIT pela primeira vez em uso.
Alguns estudiosos chamaram o JIT de “processo de supermercado”. OHNO teve ideia baseado nos comentários de uma pessoa que havia visitado os EUA e que havia descrito o funcionamento de supermercado: manter apenas o suficiente para atender a demanda por alguns dias.
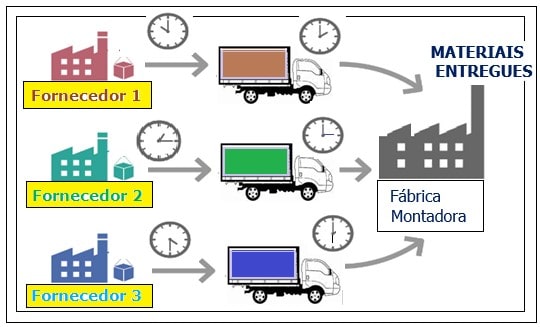
Na TOYOTA, mesmo não havendo o risco que o estoque da empresa tivesse data de validade, não havia recursos para manter um grande volume disponível como a FORD. Por ser de pequeno porte, a TOYOTA, precisava segurar o seu limitado capital de giro. Assim, da mesma maneira que o “supermercado” americano, onde os itens são colocados em prateleiras apenas na quantidade necessária para repor aquilo que os consumidores compravam, a TOYOTA internamente criou “supermercados” que reabasteceriam a linha de produção quando necessário.
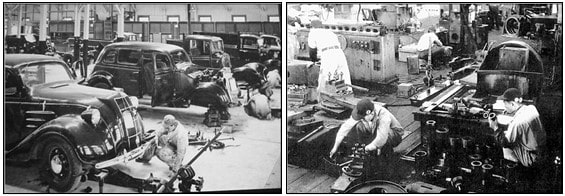
A soma das ideias de KIICHIRO TOYODA e os trabalhos de EIJI TOYODA e TAIICHI OHNO desenvolveram um processo de fabricação eficiente e com poucos defeitos. Eles criaram o que se conhece no presente como o SISTEMA TOYOTA DE PRODUÇÃO (STP). Hoje, o JUST-IN-TIME é parte dos métodos de diversas empresas no Japão e no ocidente para a obtenção de VANTAGEM COMPETITIVA.
– Vantagens do JUST IN TIME
- Os estoques menores reduzem os custos de produção e diminuem a necessidade de grandes instalações físicas, como armazéns e depósitos.
- A menor circulação de produtos e matérias primas pela fábrica permite um melhor controle e a centralização da produção.
- Custos menores implicam em preços finais mais competitivos fazendo com que a empresa ganhe mercado.
- Qualidade, Flexibilidade, Velocidade e Confiabilidade.
– Desvantagens do JUST IN TIME
- Pequenos imprevistos podem causar grandes estragos. Pelo fato de não haver estoques, o atraso de um fornecedor pode paralisar a fábrica ou prejudicar o planejamento.
- Como há poucos produtos prontos estocados, a empresa nunca está pronta para fazer uma grande entrega imediata ou de emergência.
Sugestão de leitura
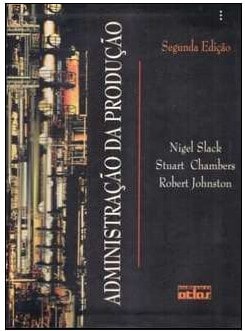
SLACK, NIGEL; CHAMBERS, STUART; JOHNSTON ROBERT. Administração da produção. Editora Atlas. Edição 2ª. São Paulo, 2002.