INTRODUÇÃO:
Em 1950, EIJI TOYODA e TAIICHI OHNO foram a Detroit conhecer o trabalho da indústria automobilística americana. De fato, eles ficaram impressionados com as instalações e o tamanho das fábricas nos EUA, a enorme quantidade de estoques, os grandes espaços disponíveis e o elevado número de funcionários. Além do mais, outro aspecto que chamou a atenção, foi o modo de produção, que atuava em um fluxo produzindo primeiro para vender depois (quando já havia grandes estoques de automóveis).
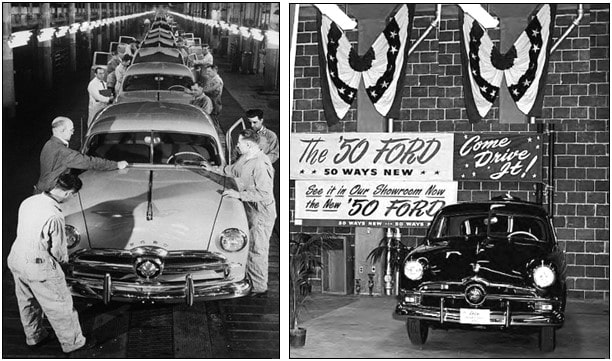
Os japoneses chegaram à conclusão que, na situação do Japão no pós-guerra, seria impraticável e não haveria condições de estabelecer uma algo semelhante ao modelo de produção que fora observado. EIJI TOYODA expôs para a direção da TOYOTA a inviabilidade da forma utilizada pelos americanos. A conclusão foi que seria preciso criar uma forma de organização do trabalho, com maior flexibilidade, que exigisse poucos estoques.
As análises também consideraram outras circunstâncias desfavoráveis e muito relevantes: o fato que o Japão tinha um mercado interno muito pequeno, o capital da TOYOTA era modesto, as matérias primas eram escassas, a obtenção de tecnologia no exterior era impossível e a possibilidade de exportação era remota.
Portanto, para ter condições de ter continuidade e competir, a empresa precisaria mudar e simplificar o que foi visto na FORD. Então, EIJI TOYODA e TAIICHI OHNO deram início a um processo de mudanças na produção, com técnicas que permitissem alterar as máquinas rapidamente durante o trabalho. Assim, seria possível ampliar a oferta e a variedade (fato que possibilitou lucros maiores). O espaço exíguo para armazenamento fez com que as mercadorias e componentes tivessem giro rápido e praticamente eliminasse os estoques.
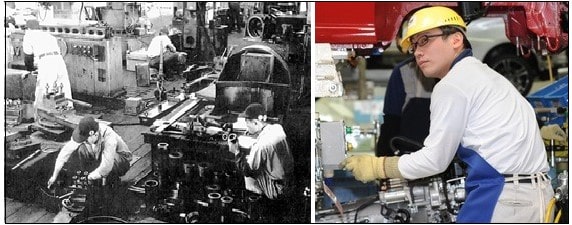
Os resultados foram muito bons. As ideias que, gradativamente foram sendo incorporadas à produção, se tornaram no cerne do modelo japonês. E, a partir da década de 1970, o sucesso do TOYOTISMO e os problemas decorrentes das crises do petróleo expandiram o modelo por todo o mundo.
15 – OS PROCESSOS PRODUTIVOS
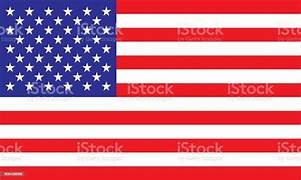
15.1 – PUSH SYSTEM ou PRODUÇÃO EMPURRADA: é ométodo americano, desenvolvido e aplicado pelo TAYLORISMO e FORDISMO. Teve a produção em massa como base e a sua importância esteve na divisão das tarefas, estudos de tempos e movimentos, na redução de tempo-padrão, na redução do custo do produto etc.
O modelo surgiu no início do Século XX, em uma época em que a demanda praticamente era infinita. A única preocupação das indústrias era ter volume para atender ao mercado. O processo produtivo no PUSH SYSTEM – PRODUÇÃO EMPURRADA começa antes da ocorrência de uma demanda pelo produto. A produção depende de uma ordem enviada anteriormente, em geral pelo sistema MRP (MATERIAL REQUIREMENT PLANNING, que pode ser entendido como planejamento das necessidades de materiais).
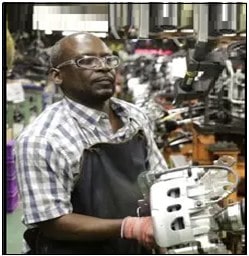
Após o recebimento da ordem, a produção é feita em lotes de produtos padronizados e não há qualquer relação com a real demanda do mercado. No PUSH SYSTEM o fluxo contínuo de produção se dá de forma isolada em cada unidade fabril da empresa.
Uma ordem de produção é enviada ao setor responsável que produz os itens e depois “EMPURRA” para a próxima etapa do processo. O controle do que deve ser produzido, a quantidade e o momento são feitos pelo MRP.
A PRODUÇÃO EM MASSA serviu, principalmente, após a II GUERRA MUNDIAL quando os recursos financeiros americanos eram grandes. Para recuperar o “tempo perdido durante a Guerra”, o mercado se tornara altamente demandante – ele havia sofrido com a retração do consumo e carência de bens.
Sistema de Produção: em série, rígida e centralizada. A demanda é baseada em previsões de vendas.
Estrutura: hierarquizada e detém as decisões de planejamento.
Divisão do trabalho: alto grau de especialização – uma única tarefa por trabalhador – pouco ou nenhum tipo de treinamento.
Produção: em grandes quantidades de um mesmo produto.
Estoques: há grandes quantidades de produtos estocados.

Vantagens e Desvantagens: o processo PUSH SYSTEM (PRODUÇÃO EMPURRADA ou MANUFATURA EMPURRADA) é um sistema tradicional e o seu conceito é que, em cada posto, seja produzida a lista de itens entregue para empurrar os itens ao posto seguinte. O PUSH SYSTEM tem como vantagens o maior controle das operações na produção, a definição dos prazos de entrega e maior preparo frente às flutuações da demanda.
Porém, suas desvantagens são a alta dependência de estoques (matéria-prima, peças e componentes durante os processos) não existe uma comunicação entre os processos e há maior dificuldade para a correção das falhas durante a produção.
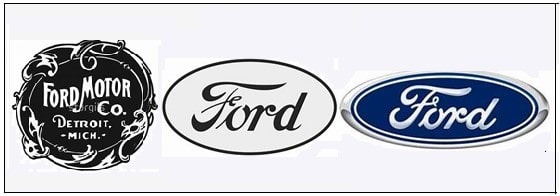
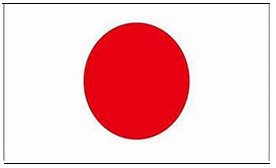
15.2 – PULL SYSTEM ou PRODUÇÃO PUXADA: exerce o controle de todas as operações fabris, sem o estoque em processo. Diferentemente do PUSH SYSTEM, o fluxo de materiais ganha relevante importância. Aqui, a demanda gerada pelo pedido cliente dá o início da produção.
Além da visita em Detroit, TAIICHI OHNO esteve em contato com uma pessoa que observou o sistema de atendimento ao varejo nos supermercados dos EUA. Ele fez uma relação entre o supermercado e o JUST IN TIME (JIT), surgindo a ideia do KANBAN, que levou dez anos para se estabelecer por completo na TOYOTA. TAIICHI OHNO observou e comparou o sistema de trabalho das indústrias e dos supermercados. Em um supermercado, o cliente para atender suas necessidades, é quem determina como deve ser o serviço de reposição de mercadorias em relação às marcas, quantidades e períodos. E, principalmente, em um regime econômico estável não é necessário manter estoques de produtos em casa.
Isto significa que o consumidor é quem “PUXA” pelas atividades daquele tipo de estabelecimento. O sistema KANBAN segue a lógica de “PUXAR” a produção. Produz somente a quantidade necessária e no momento necessário de modo a atender à demanda dos centros consumidores.
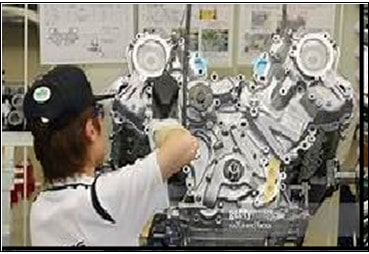
O método PULL SYSTEM (PRODUÇÃO PUXADA) é oposto ao tradicional. A operação anterior EMPURRA o resultado de sua produção para a operação seguinte. Estendendo-se este conceito a toda empresa, conclui-se que, na PRODUÇÃO PUXADA, é o cliente quem decide o que se vai ser produzido, pois, o processo de PUXAR a produção transmite a necessidade de demanda específica a cada elo da corrente.
Estes estudos redundaram em um sistema de administração da produçãocontrolada através de cartões (KANBAN). Assim como em qualquer outro sistema, o objetivo é aumentar a produtividade e reduzir os custos através da eliminação de todas as funções desnecessárias ao processo produtivo. Portanto, no sistema puxado, a produção tem por base uma demanda real, não em previsões. Este sistema ajuda a reduzir a superprodução e manter o estoque em níveis ideais.
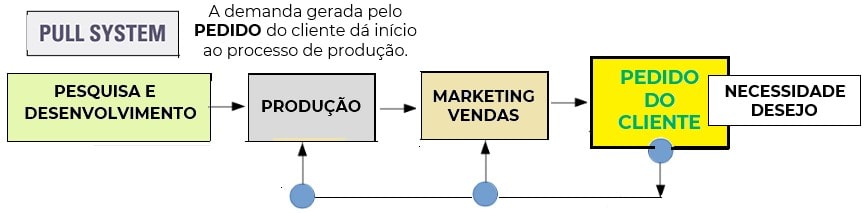
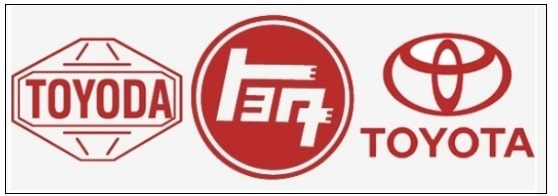
Sistema de Produção: Flexível e versátil.
Estrutura: tem por base a inovação, gestão do trabalho e mecanismos de controle interno. Contudo, o LAY OUT permite flexibilidade e a participação de todos.
Divisão do trabalho: todos os são multitarefas, apenas um operário controla várias máquinas e, assim, é possível reduzir o número de trabalhadores. Há a educação continuada (treinamento constante) e estabilidade (emprego vitalício).
Produção: é diversificada pelas demandas dos consumidores. Estoques: é o menor possível e deverá se adequar ao nível de demanda.
Vantagens e Desvantagens: no processo PULL SYSTEM (PRODUÇÃO PUXADA ou SISTEMA PUXADO) o fluxo dos materiais é de grande importância e o acúmulo de materiais entre os processos é visto como DESPERDÍCIO. O foco do sistema é reduzir estoques e evitar superproduções. Desta forma, a PRODUÇÃO PUXADA só é acionada se houver pedido. Cada processo PUXA peças, componentes e materiais do processo anterior. O PULL SYSTEM tem como VANTAGENS e redução dos estoques, redução de custo operacional, maior qualidade e a redução dos custos de produção.
Mas, suas DESVANTAGENS são a baixa produção em fases de pouca demanda, a produção é influenciada por fontes internas e externas e tem muita dependência da pontualidade dos fornecedores.
16 – FLUXO DE MATERIAIS E INFORMAÇÕES (M&I)
O MAPEAMENTO DO FLUXO E VALOR (VSM – VALUE STREAM MAPPING) é uma ferramenta que traz todos os processos e mostra o fluxo de materiais, informações, pessoas e o recebimento do valor acordado. Na TOYOTA é conhecido como FLUXO DE MATERIAIS E INFORMAÇÕES (M&I). Atua como um cronograma compreendendo, desde a emissão do pedido até a entrega do produto . É útil para reduzir o (*) LEAD TIME e eliminar qualquer atividade sem valor agregado. O M&I permite aproveita para visualizar, analisar e compreender o estado atual e o futuro desejado de qualquer processo. É bem simples de ser entendido e identifica DESPERDÍCIOS e gargalos no processo.
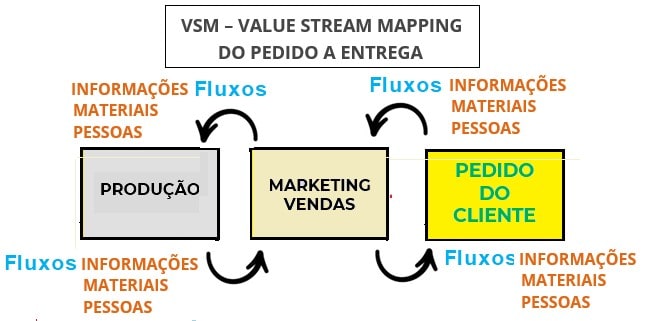
(*) LEAD TIME: na área de produção é o tempo necessário para percorrer todo o ciclo de produtivo envolvendo desde a emissão do pedido do cliente até a entrega do produto. A redução do LEAD TIME possibilita a redução de custos, a otimização dos processos, diminui desperdícios e aumenta a satisfação dos clientes.
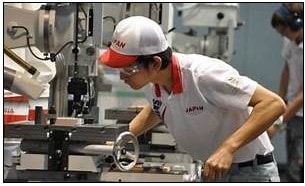
Sugestão de Leitura
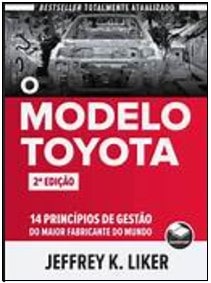
LIKER. JEFFREY K. O Modelo Toyota – 14 Princípios de Gestão do Maior Fabricante do Mundo. Editora Bookman. Edição 1ª. Porto Alegre, 2005.
LIKER. JEFFREY K. FRANZ, JAMES K. O Modelo Toyota de Melhoria Contínua: Estratégia – Experiência Operacional – Desempenho Superior. Editora Bookman. Edição 1ª. Porto Alegre, 2012.