INTRODUÇÃO:
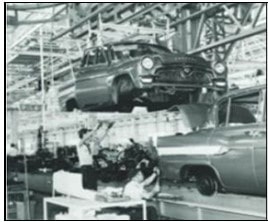
Durante os anos 1960, o processo desenvolvido pela TOYOTA foi evoluindo com muita eficiência e qualidade. Mas, era preciso ampliar o mercado para fora do Japão.
As exportações do TOYOTA CROWN,feitas para os EUA em 1957, não foram bem-sucedidas – o público americano sempre foi avesso aos carros pequenos. A empresa passou a efetuar pesquisas de mercado e atualizar o DESIGN de seus veículos.
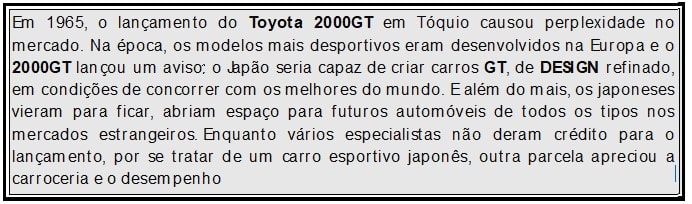
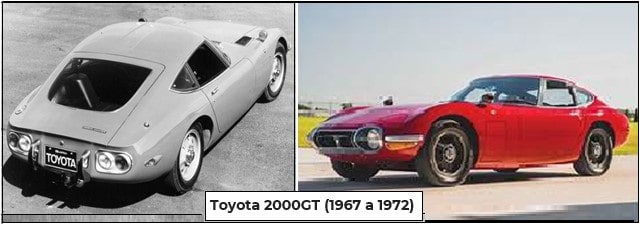
Assim, a linha de produção nos moldes do LEAN MANUFACTURING e a modernização dos produtos fariam da empresa uma das maiores montadoras do mundo na década de 1970.
A FILOSOFIA DE TRABALHO – ZERO
O maior objetivo da TOYOTA, na opinião de muitos analistas, é baixar para ZERO e eliminar os DESPERDÍCIOS de todas as formas e em todos os locais. Esta proposta envolve a superprodução, tempo de espera, transporte sem necessidade, estoque desnecessário, movimentação sem justificativa e defeitos.
Praticamente, o tudo o que é fabricado segue baseado na PRODUÇÃO POR DEMANDA (puxada), utilizando o JIT apoiado no método KAMBAN. Caso algum modelo tenha uma baixa procura, a produção da série é reduzida minimizando o estoque quase a ZERO.
O JIT traz as matérias primas e demais materiais diretamente para a linha de produção. Portanto, o custo referente a estocagem é ZERO ou quase nulo. O método KAMBAN ordena as peças e as tarefas nas linhas de produção ZERANDO problemas burocráticos e conflitos dentro da hierarquia.
O rigor na manutenção regular das máquinas e equipamentos permite que não ocorra panes e nenhum tipo de interrupção no processo fabril.
O rigor com a QUALIDADE durante a produção permite DEFEITOS ZERO. Nenhum veículo é vendido ou entregue sem estar perfeito. Desta forma, a imagem da empresa não sofre desgastes com custos de RETRABALHO, reparos, RECALL ou indenizações. É o que garante a satisfação dos consumidores.
Esta FILOSOFIA DE TRABALHO também levava em conta o respeito pelas pessoas. O STP valorizava o respeito por todos os elementos humanos (as pessoas) envolvidas no processo: funcionários, fornecedores e clientes. Como resultado, houve a formação de um local de trabalho seguro, voltado para o crescimento e a promoção de bons relacionamentos.
8 – KAIZEN
O conceito da palavra, de origem japonesa, significa melhoria (mudança para melhor,melhoria contínua, gradual na vida em geral: pessoal, familiar, social e no trabalho).
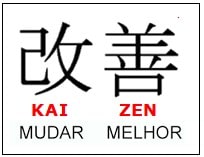
Hoje melhor do que ontem, amanhã melhor do que hoje!
A frase resume o KAIZEN, que supõe que cada aspecto da nossa vida merece ser melhorado constantemente e difunde como conceitos base: a qualidade, o esforço e a voluntariedade em mudar no ambiente organizacional com o envolvimento dos empregados.
A introdução do KAIZEN na administração da TOYOTA foi feita por TAIICHI OHNO. Sua origem está nos setores operacionais da manufatura com a filosofia de evitar qualquer DESPERDÍCIO e a MELHORIA CONTÍNUA (passo a passo, sem ser radical). O KAIZEN atua como ferramenta de redução de custos com a melhoria das rotinas pela correção das causas das falhas ocorridas.
Os resultados esperados são a redução de custos, envolvimento do pessoal na melhoria contínua das rotinas, aumento do senso de responsabilidade para transformar o quadro de funcionários em “solucionadores” de problemas.
8.1 – KAIZEN DE MANUTENÇÃO: é um trabalho diário com o imprevisível. São ações urgentes e imediatas diante de inevitáveis erros, anomalias, defeitos, mudanças e variações do dia a dia para que se cumpra o padrão esperado para (considera produtividade, qualidade, custo e segurança).
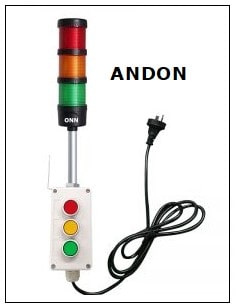
Na TOYOTA há um alto nível de atividade – incluindo as reações aos frequentes puxões na ANDON por trabalhadores da linha de produção por toda a fábrica diante do primeiro sinal de situações que estejam fora do padrão. É um trabalho de alta intensidade para solucionar problemas que possam paralisar a linha de produção.
8.2 – KAIZEN DE MELHORIA: é o trabalho de manter os padrões e também a busca pela sua melhoria: todos os funcionários tem em mente a busca pela perfeição – TUDO deve ser aprimorado.
9 – YAMAZUMI
A palavra YAMAZUMI no idioma japonês significa “Empilhar”. A metodologia ou gráfico YAMAZUMI identifica pontos de desperdícios que não agregam valor ao produto e que geram atrasos no processo. Através desta metodologia é possível graficamente de identificar, analisar o processo e tomar ações para conter ou eliminar DESPERDÍCIOS.
O desenvolvimento de processo é “empilhado” para mostrar os tempos de ciclo e o processo do operador identificando os passos que agregam ou não valor para mostrar desperdícios, com cores:
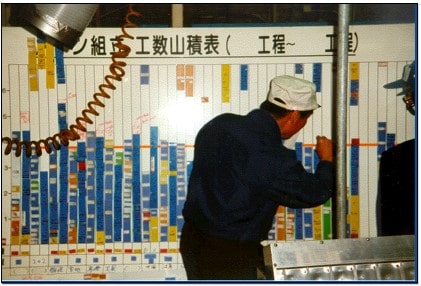
- VERMELHO – resíduos no processo – o bloqueio ou o modo de falha.
- LARANJA – passos que são necessários para o processo, mas realmente “não agregam valor”.
- VERDE – etapas que fazem uma diferença real – as etapas de execução.
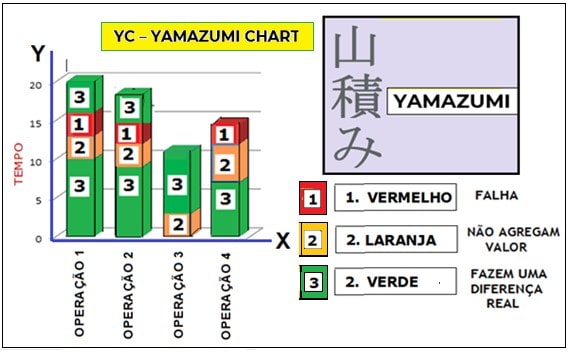
VANTAGENS: é visual e é uma forma simples de identificar gargalos (falhas ou GAPS), é útil indicando o caminho para a melhoria contínua (KAIZEN), é visível para todos e mostra aspectos que podem ser estudados e melhorados. O gráfico de barras “empilhadas” pode apresentar diversos aspectos de um processo, como:
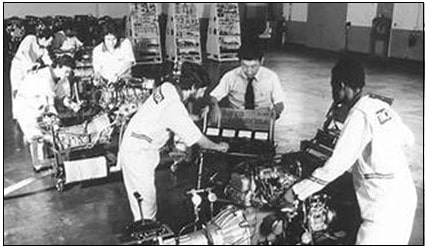
- Tempo de espera e tempo de caminhada.
- Tempo de processamento.
- Tempo da máquina.
- Tempo de preparação.
- Retrabalho/Reparo.
- Atrasos e desperdícios.
- Aguarda o tempo do KANBAN.
- Traz valor Agregado.
- Não Agrega Valor.
10 – JIDOKA (AUTONOMAÇÃO)
Foi a técnica criada na máquina de tear automática de SAKICHI TOYODA que interrompia o funcionamento sempre que um fio se rompesse (um dispositivo automático que parava a máquina se ocorresse algum erro). O problema do tear automático era que ele continuava funcionando, mesmo com o rompimento do fio. O defeito só era notado quando o processo estivesse finalizado com um tecido defeituoso. Então, era preciso ter um trabalhador acompanhando e vigiando a máquina que, diante de qualquer problema deveria parar o processo.
Em 1924 SAKICHI apresentou um tear com um dispositivo que parava a máquina ao detectava o rompimento do fio, ou o fim da linha ou se a quantidade pretendida fosse alcançada. Com este processo, SAKICHI pôde liberar o trabalhador de permanecer vigiando a máquina à espera da ocorrência de algum problema.
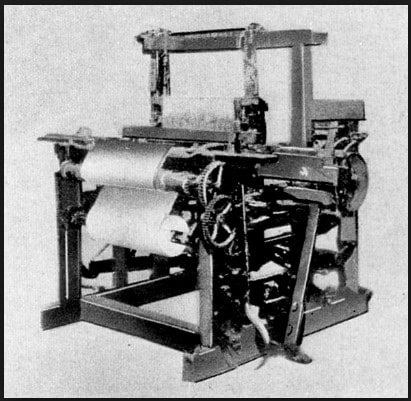
TAIICHI OHNO aplicou este princípio ao STP com base numa questão:
Por que na TOYODA um operário operava simultaneamente até 40 máquinas e na TOYOTA MOTOR cada operário opera apenas uma máquina? As máquinas na TOYOTA quando o processamento estivesse terminado ou quando um fato anormal acontecesse.
Caso aconteça alguma situação anormal a máquina interrompe o trabalho e qualquer operador pode parar a linha de produção inteira ao detectar um erro e iniciar o processo dos “5 PORQUÊS?” (FIVE WHY’S). Faz parte do comprometimento de não enviar para operação ou processo seguinte uma peça, parte ou trabalho fora do padrão: é uma das regras básicas do TPS – a qualidade é verificada durante o processo fabril.
A parada é seguida de um alerta ou sinal dado pelo operador pelo acionamento de botões ou cordas (ANDON) na linha de montagem. Uma equipe é acionada sobre o erro até chegar à sua CAUSA RAIZ, evitando assim que este problema ocorresse novamente e impedir a geração e a propagação dos defeitos.
O JIDOKA permite eliminar qualquer anormalidade no processamento. Portanto, previne produtos defeituosos, elimina superprodução e foca a atenção na compreensão do problema para assegurar que ele não se repita. Consiste em:
1 – Detectar a anormalidade.
2 – Parar.
3 – Consertar ou corrigir a condição imediatamente.
4 – Investigar a causa raiz para instalar uma contramedida.
Muitas vezes, alguns especialistas denominam o JIDOKA (AUTONOMAÇÃO) como “AUTOMAÇÃO COM TOQUE HUMANO“.
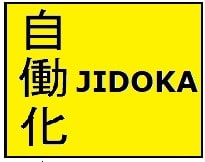