INTRODUÇÃO:
Desde a criação do LEAN MANUFACTURING até a TOYOTA se tornar a maior montadora do mundo, a história foi longa. O LEAN não nasceu da noite para o dia e levou tempo para que a empresa se desenvolvesse e alcançasse o sucesso com sua forma de produção. O LEAN MANUFACTURING só se solidificou na década de 70 e aproveitou também os efeitos que o CHOQUE DO PETRÓLEO causou nos países ocidentais.
FERRAMENTAS LEAN: FIVE WHY’S, (5 POR QUES), FILOSOFIA 5S, JIT (JUST IN TIME), MILK RUN, PADRONIZAÇÃO DE ATIVIDADES, MUDA, SMED (SINGLE MINUTE EXCHANGE OF DIE – Troca rápida de Ferramentas ou TRF), KANBAN, KAIZEN,YAMAZUMI,JIDOKA – AUTONOMAÇÃO, HEIJUNKA, TAKT TIME,POKA YOKE, PULL SYSTEM, M&I – FLUXO DE MATERIAIS E INFORMAÇÕES, MAPEAMENTO DE FLUXO E VALOR e PET –PRÁTICAS EMPRESARIAIS TOYOTA.
4 – MILK RUN
A TOYOTA também observou o exemplo americano e adaptou para a indústria uma prática dos antigos leiteiros: o MILK RUN (o caminho do leite). Eles deixavam galões vazios na porta das fazendas fornecedoras e levavam galões cheios no lugar, tendo, assim, a matéria prima no momento que desejavam.
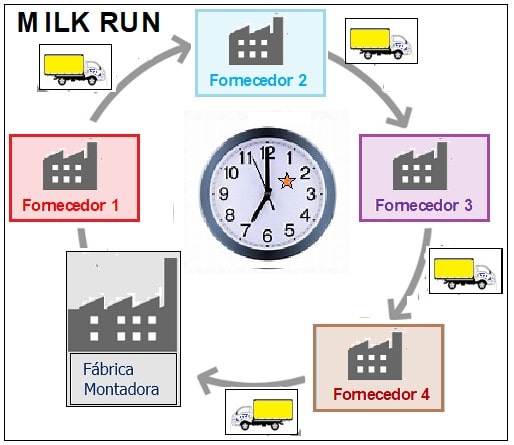
Os japoneses aperfeiçoaram o processo para a Indústria visando diminuir o tempo e custo de produção com as coletas programadas de materiais. A tarefa é feita com um único veículo de um operador logístico nas coletas em um ou mais fornecedores. A entrega dos materiais no destino deverá sempre ter horário de início e horário de entrega previamente estabelecidos.
5 – PADRONIZAÇÃO DE ATIVIDADES
O LEAN MANUFACTURING também tem como um dos seus objetivos obter a PADRONIZAÇÃO DO TRABALHO. Ela é aplicada para alcançar a redução de custos da produção e do PRODUTO, melhorando ou mantendo sua qualidade. Ou seja, o intuito é estabelecer procedimentos precisos, métodos claros, específicos, compreendidos e perfeitamente alinhados entre todos os executores. A PADRONIZAÇÃO procura fazer com que o trabalho de cada um deles siga o mesmo processo. Ela reduz a variabilidade, segue normas, facilita os programas de treinamento, de novos operadores, minimiza os riscos acidentes, permite melhorias e eleva os cuidados com a qualidade.
6 – SMED (SINGLE MINUTE EXCHANGE OF DIE)
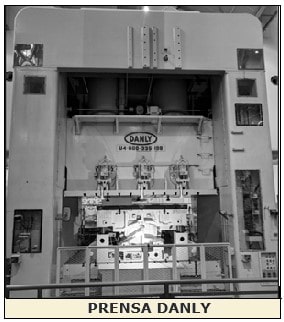
Em visitava aos EUA em 1955, TAIICHI OHNO verificou sobre a maneira como as prensas de estampagem DANLY eram capazes de terem as matrizes trocadas com rapidez. A TOYOTA adquiriu as prensas e procurou trabalhar para melhorar o (*) TEMPO DE TROCA.
No mesmo ano, em um treinamento, SHIGEO SHINGO abordou o conteúdo engenharia industrial e melhorias na TOYOTA criando o SMED (SINGLE MINUTE EXCHANGE OF DIE) para a redução do (*) TEMPO DE SETUP de máquinas ou de linhas de produções.
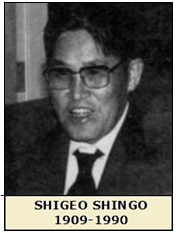
(*) TEMPO DE TROCA: é o tempo necessário para uma máquina seja convertida da produção da última peça para a primeira peça da próxima produção.
(*) TEMPO DE SETUP: é o tempo em que a produção é interrompida para a troca de estampas ou para o ajuste de equipam
O JUST-IN-TIME aumentou a necessidade de produção de lotes menores e frequentes. Esta mudança de formato exige configurações aceleradas para manter a flexibilidade, atender às demandas dos clientes e permanecer competitivo. Assim, era imprescindível diminuir ao máximo o TEMPO DE TROCA e o TEMPO DE SETUP na troca das matrizes nas prensas.
As matrizes das máquinas de estampagem eram as ferramentas mais difíceis de mudar. Elas produziam as peças de carroceria e obrigatoriamente deveriam ser trocadas para cada modelo. Além do mais, eram pesadas e deveriam ser montadas nas máquinas de estampar (prensas) com tolerâncias inferiores a um milímetro (se houvesse alguma falha, o metal a ser estampado correria o alto risco de enrugar ou derreter, sob o intenso calor e pressão.
O processo de SHIGEO SHINGO permitiu reduzir o TEMPO DE TROCA para atender as demandas do JIT. A princípio, em menos de 10 minutos, diminuindo o período em que a produção e preparação do maquinário e das ferramentas para executar o serviço permaneciam paralisadas. Com os anos o processo progrediu: o que levava horas no início caiu para 180 segundos a partir de 1990.
O SMED é conhecido como TROCA DE MATRIZ E MANUTENÇÃO EM UM MINUTO ou TRF (TROCA RÁPIDA DE FERRAMENTAS).
7 – KANBAN
O KAMBAN teve origem na TOYOTA e remonta ao início da década de 1950. Em japonês, a palavra significa um marcador que poderá ser um cartão, sinal ou placa.
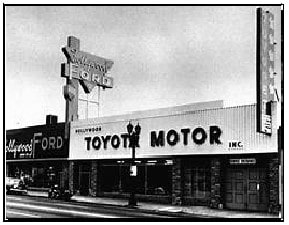
É uma ferramenta que administra a produção e autoriza a produção e a movimentação do material no sistema JIT para controlar a ordem e a sequência dos trabalhos. Também tem por finalidade assinalar a necessidade de mais material e assegurar que tais peças sejam produzidas e entregues a tempo de garantir a fabricação ou a sequência da montagem.
Os cartões descrevem o trabalho real que está transitando pelo processo e para solicitar componentes a outras equipes da mesma linha. Os cartões mostram o andamento dos fluxos de produção em série e nos cartões são colocadas todas as indicações sobre uma determinada tarefa:
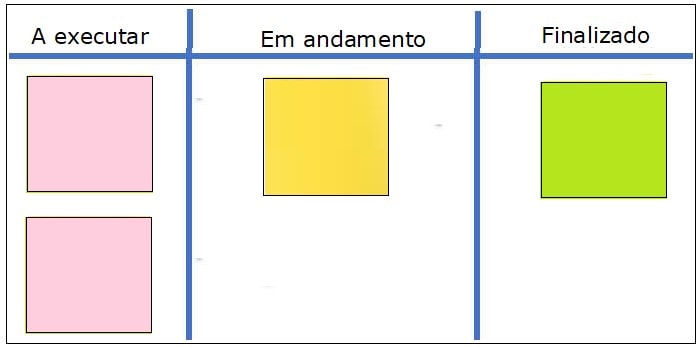
O resultado será que todos os centros de fabricação receberão no momento exato as quantidades necessárias de itens para que se cumpram os objetivos do. Ou seja, é um sistema de informação através de CARTÕES que que permitem dividir o trabalho em segmentos e controlar as quantidades a serem produzidas. O sistema KANBAN permite o controle detalhado da produção com as informações sobre quando, quanto e o que produzir. Foi inicialmente aplicado em empresas japonesas de fabricação em série e está ligado ao JUST IN TIME.

O e-KANBAN: o KANBAN eletrônico é utilizado em substituição ao KANBAN físico. O seu uso evita alguns problemas comuns tais como a perda dos cartões, extravios, dificuldade na leitura e interpretação e proporciona atualização mais rapidez que o quadro de tarefas.
Sugestão de Leitura
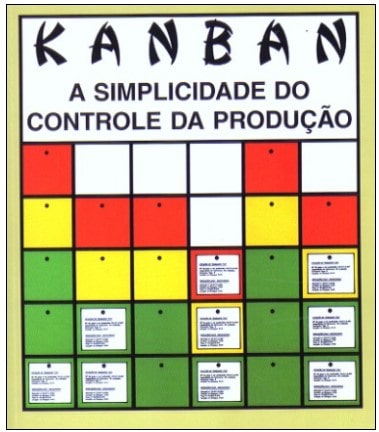
MOURA, REINALDO A. KANBAN – A simplicidade do CONTROLE da PRODUÇÃO. Editora IMAM. São Paulo, 2003.
FERREIRA, ADEMIR ANTONIO; PEREIRA, MARIA ISABEL Gestão Empresarial: de Taylor aos nossos dias. Editora Pioneira, Edição 1ª. São Paulo, 1997.
LIKER ,JEFF; KARYN ROSS; O Modelo Toyota de Excelência em Serviços: A Transformação Lean em Organizações de Serviço. Editora Bookman; Edição 1ª. Porto Alegre, 2019.