INTRODUÇÃO:
O SISTEMA TOYOTA DE PRODUÇÃO também é conhecido por PRODUÇÃO ENXUTA ou LEAN MANUFACTURING ou STP. Durante a guerra, quando a TOYOTA fabricava caminhões para o exército, sua produtividade era muito baixa e havia uma enorme falta de recursos. E mesmo se os recursos estivessem disponíveis havia outro agravante. Segundo pesquisas feitas em 1937, um operário alemão ou americano produzia três vezes a mais em comparação com o que produzia um operário japonês. Ou seja, a ideia foi que ao se ELIMINAR A PERDA, a PRODUTIVIDADE poderia ser maior.
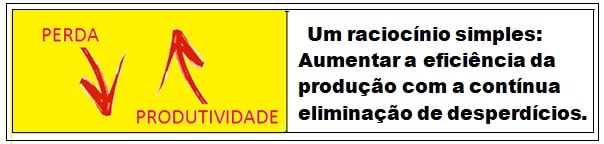
AS IDEIAS DO SISTEMA TOYOTA
Depois da visita à FORD em 1950, em 1950, EIJI TOYODA e TAIICHI OHNO concluíram que a PRODUÇÃO EM MASSA não funcionaria no Japão. Por décadas, as empresas ocidentais diminuíram os custos com a PRODUÇÃO EM MASSA de pouca variedade de carros. Isto era um estilo americano de trabalho. Com base nestas observações, surgiu o SISTEMA TOYOTA DE PRODUÇÃO. O pensamento era cortar custos, produzindo um pequeno número de muitos tipos de carros em função do perfil do mercado japonês no pós-guerra:
– O mercado doméstico era pequeno e exigia uma variedade muito grande de tipos de produtos e havia a dificuldade em importar matérias-primas
– A compra de tecnologia no exterior era economicamente inviável.
– A possibilidade de exportação era remota.
(*) PRODUÇÃO EM MASSA: a forma de organização e sistematização da produção desenvolvida por FREDERICK TAYLOR (a ADMINISTRAÇÃO CIENTÍFICA) procurou a maximização da produção e o máximo aproveitamento da mão de obra para reduzir custos e elevar os lucros. Tomando por base as ideias de TAYLOR, HENRY FORD desenvolveu o método da linha de montagem (o FORDISMO). O objetivo foi reduzir o custo unitário dos produtos pela produção em larga escala (em MASSA), divisão do trabalho e especialização onde o operário desenvolvia uma única tarefa. Mas, o sistema da FORD tinha de trabalhar com grandes estoques peças e materiais, altos lotes de produção e grandes instalações físicas.
AS CARACTERÍSTICAS DO TOYOTISMO
1 – STP (Sistema Toyota de Produção): omodelo produtivo criado por TAIICHI OHNO, EIJI TOYODA e SHINGEO SHINGO, foi sendo desenvolvido entre 1948 e 1975, idealizou a produção de lotes pequenos para permitir maior variedade. Outras características do STP: ter os operários MULTIFUNCIONAIS, com a capacidade de desenvolver mais de uma única tarefa e operar diversas máquinas. Havia uma grande preocupação com a qualidade e o STP trabalharia com pouco estoque, fluxo de caixa curto e eficiência na produção.
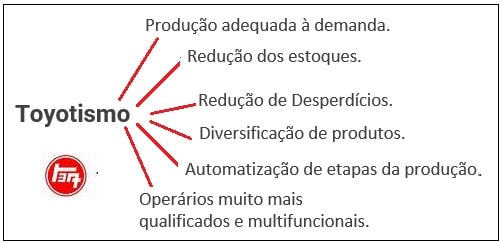
2 – Os 7 Tipos de DESPERDÍCIOS: após a visita à fábrica da FORD em Detroit EIJI TOYODA e TAIICHI OHNO concluíram que o principal problema existente no modelo americano de produção era o desperdício de recursos.
TAIICHI OHNO teve a percepção que o melhor era esperar receber encomendas para iniciar a produção a fim de economizar em aluguéis de armazéns. Ao poupar espaço na estocagem de matérias-primas e materiais, a fábrica aumentava a produtividade ao diminuir DESPERDÍCIOS, o tempo de espera, a superprodução e os problemas no transporte.
A eliminação de DESPERDÍCIOS: a preocupação estava nas atividades da fábrica com o objetivo de reduzir ao máximo qualquer trabalho que não agregasse valor ao produto. Assim, o STP (denominado (*) LEAN MANUFACTURING ou Produção Enxuta criado em 1950), pode ser considerado como sendo um sistema de gestão focado na eliminação de desperdícios.
- Produzir produtos defeituosos significa desperdiçar materiais, mão-de-obra, movimentação de materiais e TEMPO.
- Superprodução: é o maior o desperdício (não produzir o que não foi vendido).
- Algumas operações em um processo nem deveriam existir.
- Transportes não agregam valor ao produto.
- Eliminar o que está em excesso, além do mínimo para executar a atividade.
- Movimentação: deslocamento de peças e processos dentro das empresas.
- Espera: materiais aguardando em filas para serem processados.
Alguns autores e estudiosos do TOYOTISMO consideram mais um desperdício: A Criatividade perdida – reuniões, planos de ação sem se concretizar a ação.
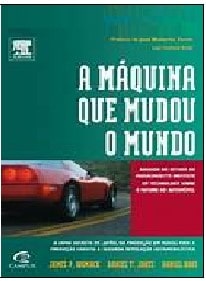
(*) o termo LEAN MANUFACTURING foi criado em 1990 pelos autores JAMES WOMACK, DANIEL JONES e DANIEL ROSS no livro “A MÁQUINA QUE MUDOU O MUNDO”. Editora Campus/Elsevier. Edição 8ª. São Paulo, 2004.
Os principais objetivos do processo de LEAN MANUFACTURING são a redução de Custos. Melhoria Contínua, Produção ágil, maior capacidade produtiva e melhor ambiente de trabalho. O LEAN MANUFACTURING segue 5 princípios básicos: Valor, Fluxo de Valor, Fluxo Contínuo, Produção Puxada e a Perfeição.
3 – A fabricação com QUALIDADE: produção com defeito ZERO. Entretanto, o sucesso destas duas ideias só estaria assegurado com o total envolvimento dos trabalhadores. A cultura contra o desperdício traz excelentes benefícios para as empresas e paras as pessoas.
4 – Os 3 MU`S:
4.1 – MURI: é a sobrecarga dos processos ou das pessoas.
4.2 – MURA: é a irregularidade ou desigualdade.
4.3 – MUDA: é o desperdício. – “Qualquer coisa que aumente o custo sem agregar valor”. MUDA é o MU mais importante, busca da eliminação total de qualquer tipo de desperdício e está dividido em 8 DESPERDÍCIOS:
4.3.1 – Superprodução: excesso de produção e grande fonte de desperdícios mostra a falta de sincronia entre processos e/ou tarefas: tempo, conteúdo, quantidade e capacidade.
4.3.2 – Tempo de espera: refere-se a materiais que aguardam em filas para serem processados.
4.3.3 – Transporte: evitar grandes distâncias a serem vencidas.
4.3.4 – Processos desnecessários: atividades ou funções que não agregam valor, características desnecessárias ao produto, competências e ferramentas de uso inapropriado (algumas operações dentro de um processo poderiam ser eliminadas).
4.3.5 – Movimentação: é considerada qualquer movimento desnecessário.
4.3.6 – Defeitos: produtos defeituosos significam o desperdício de materiais, mão-de-obra, movimentação e outros.
4.3.7 – Estoque: fonte de desperdícios, o estoque imobiliza o capital.
4.3.8 – Conhecimento sem ligação: falta de comunicação dentro de uma empresa ou entre a empresa e seus fornecedores.
A gestão para ter grande potencial de resultado precisa ser equilibrada e ela compreende atividades que agregam valor, que transformem matérias primas e informações em produtos que o cliente necessita. O intuito foi reduzir as atividades sem valor agregado: as que não agregam nada, que apenas consomem recursos e que não contribuem diretamente para o produto.
5 – GEMBA: a palavra em japonês é traduzida como “o lugar real”. Na LEAN MANUFACTURING é entendida como onde o trabalho é realizado, a área de produção, ou seja, o CHÃO DE FÁBRICA. Uma caminhada no GEMBA é a ação de ir até a área onde o trabalho é realizado e observar, tentar entender o trabalho, fazer perguntas aos trabalhadores e aprender para fazer melhorias no processo.
6 – Produção FLEXÍVEL: no sistema produtivo do TOYOTISMO as linhas de montagem não são estáticas e podem ser modificadas constantemente segundo a necessidade do momento (fabricar produtos em pequenos lotes conforme encomendas).
7 – Mecanização FLEXÍVEL: esta foi uma dinâmica oposta à automação rígida do sistema da FORD. A mecanização flexível visa em produzir somente o necessário. Neste processo as máquinas, que tradicionalmente executam apenas uma única função, foram trocadas por um maquinário de múltiplas funções para produzir pequenos lotes de diferentes itens de acordo com as encomendas.
8 – Mão de Obra MULTIFUNCIONAL: com base na MECANIZAÇÃO FLEXÍVEL e na produção para mercados muito segmentados, a mão-de-obra não podia ser especializada com funções únicas e restritas conforme o modelo FORDISTA.
TAIICHI OHNO promoveu a racionalização da força de trabalho ao agrupar os operários em equipes com um líder ao invés de um supervisor. As equipes receberam um conjunto de tarefas de montagem e trabalhavam de forma coletiva para que a execução fosse da melhor forma possível.
Ao mesmo tempo o Líder trabalha junto com o grupo em qualquer eventualidade. As equipes também faziam tarefas simples de manutenção de seus próprios equipamentos e controle de qualidade. Por exemplo, TAIICHI OHNO treinou os operários para que eles mesmos fizessem mudanças nos moldes e prensas da lataria dos veículos eliminando a dependência de especialistas para essa operação.
Na década de 1950 a TOYOTA trocava os moldes das prensas em 3 minutos (uma tarefa que anteriormente levaria um dia inteiro de trabalho). Os próprios funcionários tinham a tarefa de fiscalizar e verificar os níveis de qualidade do que era fabricado e diminuíram o nível de defeitos.
9 –QUALIDADE TOTAL: se na PRODUÇÃO EM MASSA da FORD a qualidade era assegurada através de controles amostrais, com a verificação em apenas alguns pontos do processo produtivo, no TOYOTISMO o rigoroso controle de qualidade acontece por meio de TODOS os trabalhadores em TODOS os pontos do processo produtivo.
Para atingir esse objetivo, os japoneses investiram na educação e qualificação. O TOYOTISMO,, em lugar de avançar na tradicional divisão do trabalho, seguiu também um caminho inverso, incentivando uma atuação voltada para o enriquecimento do trabalho (ou enriquecimento da tarefa).
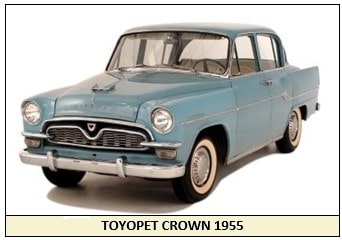
O SEGREDO DO SUCESSO
Mesmo com a situação do pós-guerra, com as condições geográficas desfavoráveis do país, com espaços exíguos, mercado consumidor pequeno, a TOYOTA evoluiu e se transformou na maior montadora de veículos do mundo.
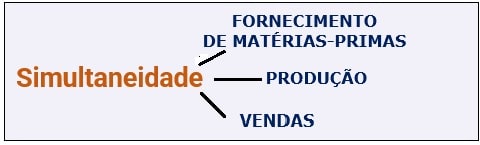
Isto se deveu aos avanços tecnológicos, aos meios de transporte e comunicação que possibilitaram a rapidez e a presteza do fluxo de materiais para a PRODUÇÃO FLEXIBILIZADA. Os sistemas de fornecimento de matérias-primas, de produção e de venda de forma simultânea explicam os resultados positivos do TOYOTISMO.
Sugestão de Leitura
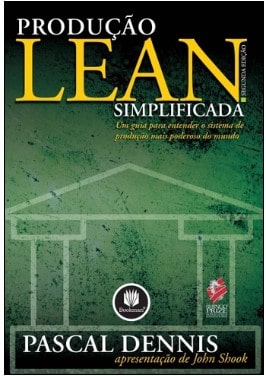
DENNIS, PASCAL. Produção Lean Simplificada: Um Guia para entender o Sistema de Produção Mais Poderoso do Mundo. Editora Bookman. Edição 2ª. Porto Alegre, 2008.
LIKER, JEFFREY K.; CONVIS, GARY L. O Modelo Toyota de Excelência em Serviços: A Transformação Lean em Organizações de Serviço. Editora Bookman. Edição 1ª. Porto Alegre, 2019.